Products
Commitment to Excellence
Uncompromising Quality in Manufacturing
M&M International sources the best raw materials for use in our products, which include drill stem safety valves (DSSV), canister valves, inside BOP valves (or IBOP valves), kelly cocks and kelly valves, safety valves, subs, mudsavers, and top drive valves. Material traceability is maintained throughout all phases of manufacturing.
Our Valve Products
What is CANISTER GUARD®?
In 1993, M&M International designed, patented, produced, and deployed the revolutionary CANISTER GUARD® valve design, which is still today the most innovative feature to ever be incorporated into a kelly, top drive, or safety valve. Over the years, M&M refined and improved the CANISTER GUARD® design to make it even more dominant. M&M currently has a patent pending on its latest iteration of the most efficient and effective well control valve design in history.
M&M International’s CANISTER GUARD® is comprised of other patented M&M technologies, namely LITE-TORC™, SURE-STOP™ and CHECK-SEAL™, along with its modular configuration of the internal parts, or “canister”, as the name implies.
M&M International’s CANISTER GUARD® reduces the need for customer rigs and locations to keep large spare valve parts inventories on hand. In most cases, CANISTER GUARD® valves utilize identical parts within each size range. This low inventory ability allows a customer to operate with one spare canister and one or two spare operating stems in inventory, if necessary. Also, the locking mechanism parts are rarely damaged and can typically be used over and over again.
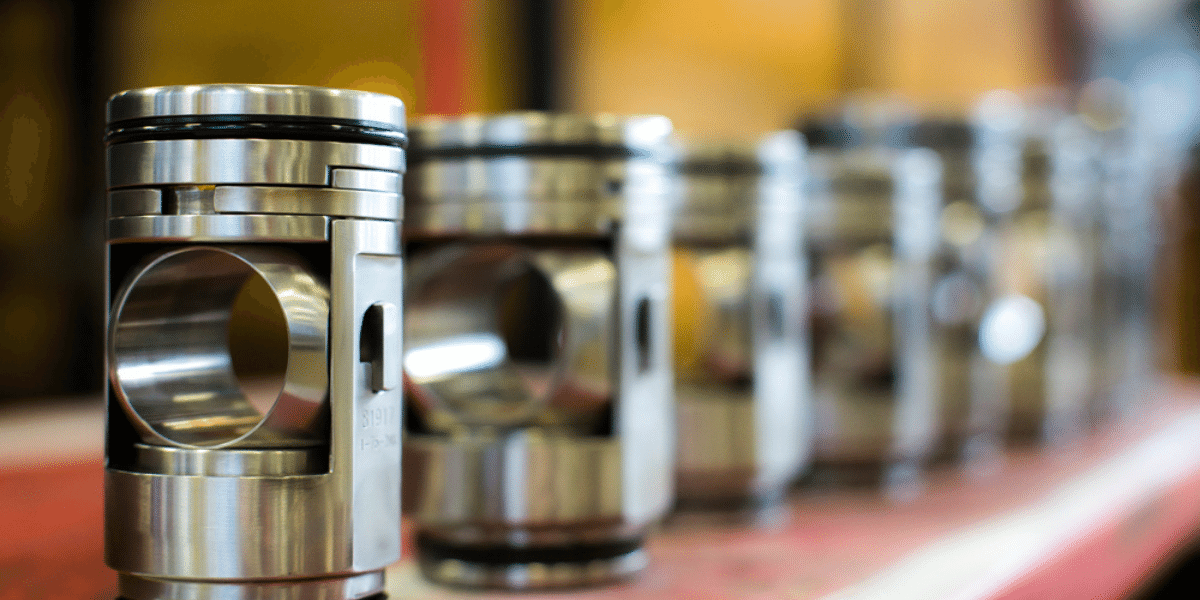
CANISTER GUARD® Design
The M&M International CANISTER GUARD® encapsulates its internal spring loading within the canister itself, which is a significant feature that cannot be overstated. During disassembly of one-piece valves made by other manufacturers, the internal spring must be compressed prior to removal of the locking mechanism.
Considering the application, it is typical for mud, cement, debris, and/or corrosion to accumulate in this area. This makes it difficult or even impossible to compress the spring enough to remove the locking mechanism from valves of this kind, even when using the special tools required by such inferior valve designs.
These and other issues can make field dressing impractical and shop dressing a much longer and more expensive process than necessary. M&M International’s CANISTER GUARD® technology completely eliminates these issues, saving both time and money.
.png?width=500&height=500&name=Cannister%20Guard%202%20(2).png)
Assembly and Disassembly of M&M International Valves
With our valves, there are no special assembly or disassembly tools required, no threaded seats to remove, and no spring tension to overcome when working with a CANISTER GUARD® valve.
-
Assembly
Assembly or redress of our valves is virtually fail-safe since all internal parts, except the operating stem assembly and locking devices (if required), can be pre-assembled and ready for quick and easy installation in the field, anywhere in the world. First, the operating stem assembly is installed in the valve body and rotated to the closed position, then the canister, also in the closed position, is inserted into the valve body and fully seated. The canister must then be locked in its position. For one-piece valves, locking segments are inserted into the body followed by the support ring and spiral retainer ring. For two and three-piece valves, the internal pin locks the canister in place. Assembly or redress is then complete.
-
Disassembly
Disassembly is just as easy. First, for one-piece valves, the locking mechanism is removed using an ordinary screwdriver and pair of spreading pliers, then the canister is tapped out through the box end of the valve using a wooden handle or dowel. For two and three-piece valves, simply removing the internal pin portion of the valve assembly will unlock the canister. Once the canister is removed, access to the operating stem is unobstructed, allowing the stem to be easily removed. Note that there are no special assembly or disassembly tools required, no threaded seats to remove, and no spring tension to overcome when working with a CANISTER GUARD® valve assembly, making CANISTER GUARD® the easiest well control valve in the industry to disassemble.
M&M International Patented Technologies
LITE-TORC™
M&M International’s LITE-TORC™ technology offers the ability to close the CANISTER GUARD® valve while under significant flow and allows the valve to be easily opened or closed under high-balanced pressure.
Utilization of the LITE-TORC™ system drastically improves the ability of a valve to be closed under heavy flow, enabling the closing of the CANISTER GUARD® valve by one man with a standard 12” hex wrench. Once the valve is closed, wellbore pressure can slowly be balanced by pump pressure to allow the valve to be re-opened with less than 30ft. lbs. of torque.
SURE-STOP™
The M&M International SURE-STOP™ technology incorporates dual interior contact points within the cage leg(s) to stop ball rotation when in the fully opened or closed position, limiting ball rotation to 90 degrees.
With SURE-STOP™, the frustrating possibilities of over or under rotation are completely eliminated, providing a seamless and hassle-free experience. Additionally, this feature plays a vital role in safeguarding the internal components of the CANISTER GUARD® from any potential washout or erosion. Trust in the power of SURE-STOP™ to deliver optimal performance and prolong the lifespan of your equipment.
CHECK-SEAL™
M&M International’s CHECK-SEAL™ technology is incorporated into all CANISTER GUARD® valves. The CHECK-SEAL™ functions as a check to maintain a pressure seal in one direction. Consequently, CHECK-SEAL™ allows wellbore pressure to bypass the lower seat, forcing a seal between the solid cross-section of the ball, which is the strongest geometry of the ball, and the upper seat.
Top End Pressure
The “cage legs” in the CANISTER GUARD® valve configuration limit the allowable travel of the upper seat, which creates a function similar to that of the CHECK-SEAL™, but in the opposite direction. When pressure from above the valve is applied to the top of the ball, the ball is able to continue to travel downward away from the pressure even after the cage legs have stopped the movement of the upper seat. As the ball moves away from the upper seat, the pressure is able to bypass the ball and instead force a pressure seal between the stronger geometry of the ball and the lower seat.